In the operation manual of the rotating torque meter UTM series, there is a following description: “Use this product without fixing the main body.”
However, there are applications that require the main body to be fixed in some cases. In this article, we will explain these cases.
First of all, what would “not fixing the main body; let it float” mean?
Let’s assume that a drive source (such as a motor) and a load device are fixed on a surface plate. Normally, each shaft rotates smoothly without eccentricity or vibration. Thus, if connecting a torque meter and shafts with the couplings, its main body is let floated. If the torque meter is fixed at this point, cumbersome shaft alignment will be required, ending up with triggering misalignments of eccentricity or deflection angle etc.
Because the UTM series is lightweight at the housing so that its own weight does not affect the torque measurement, the torque can be measured accurately even if it is let floated.
In this case, be sure to use the single type (single joint) couplings between the devices.
This method allows us not only the shaft alignment and the centering with no difficulty, but also the installation with ease. As the misalignments of eccentricity and deflection angle are absorbed by the two couplings, even fine tunings are unnecessary as long as it is within the allowable range.
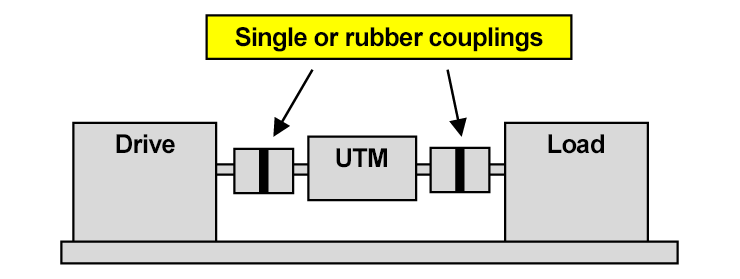
Additionally, there is another description that “never use double or Oldham couplings.” This is written in the sense that if more than two joints, such as double or bellows are used, they may bounce around and break when the torque meter body is floated, and if separable items such as Oldham or jaw couplings are used, they may induce dropout and scatter, which is very dangerous.
Of course, since equipment speed, measurement conditions and required performance are not uniform, there are instances where the main unit should be fixed or double couplings, etc. should be used.
These cases will be explained below.
The installation method when the loads are swapped frequently
In-process inspection equipment may require frequent load changes, so an Oldham or jaw type, which can be separated from the load and shaft, may be desirable.
When a separatable coupling is used, be sure to fix the main body to use. In that case, be sure to use a double type coupling between the drive side and the fixed torque meter.
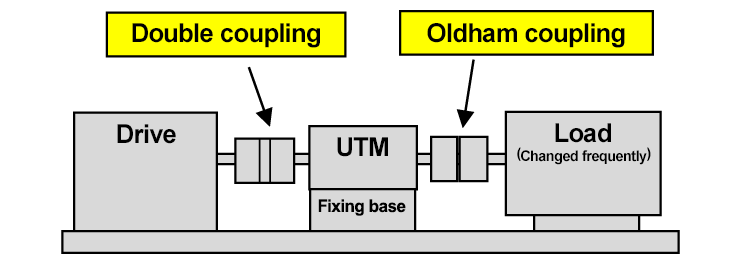
For such applications, a centering type UTM is also available.
For the centering location type, the position of the shaft center is determined by the in-row.
This has the advantage that fine adjustments with a positioning of a shaft can be omitted during equipment assembly.
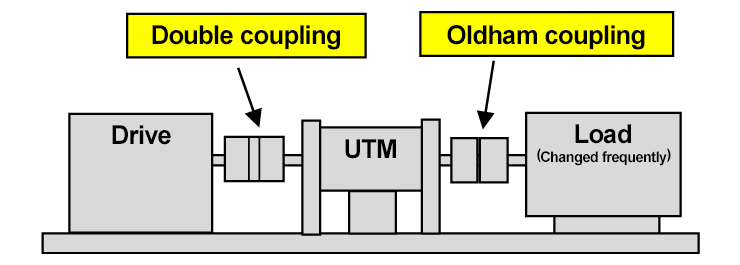
If there is a risk of excessive load being applied to the shaft when installing a load, a bearing post should be provided and an angular bearing or cross roller bearing should be used and designed to receive the axial (thrust) force.
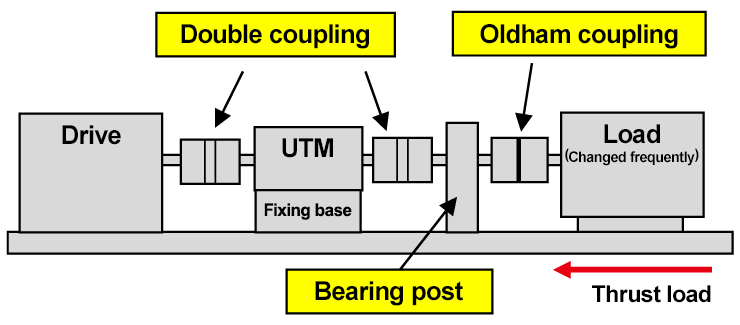
The installation method when the load or the drive vibrates
When connecting an engine or other devices with large vibrations, use a bearing that can withstand high loads so that the vibration is not transmitted to the torque meter.
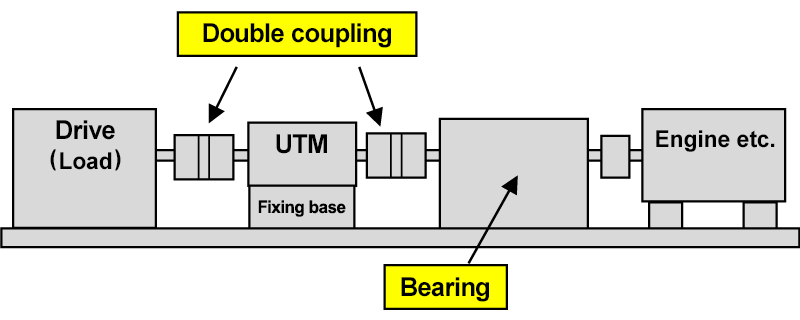
Installation method when letting the torque meter rotates with high-speed
To let the torque meter rotate with high-speed, a critical speed (a rotation speed that coincides mechanistic resonance) should be aware.
If there is an overlap between the critical speed and the rated operating speed, equipment damage may result. Increasing the critical speed requires an inscrease in stiffness, which may require the main body to be fixed.